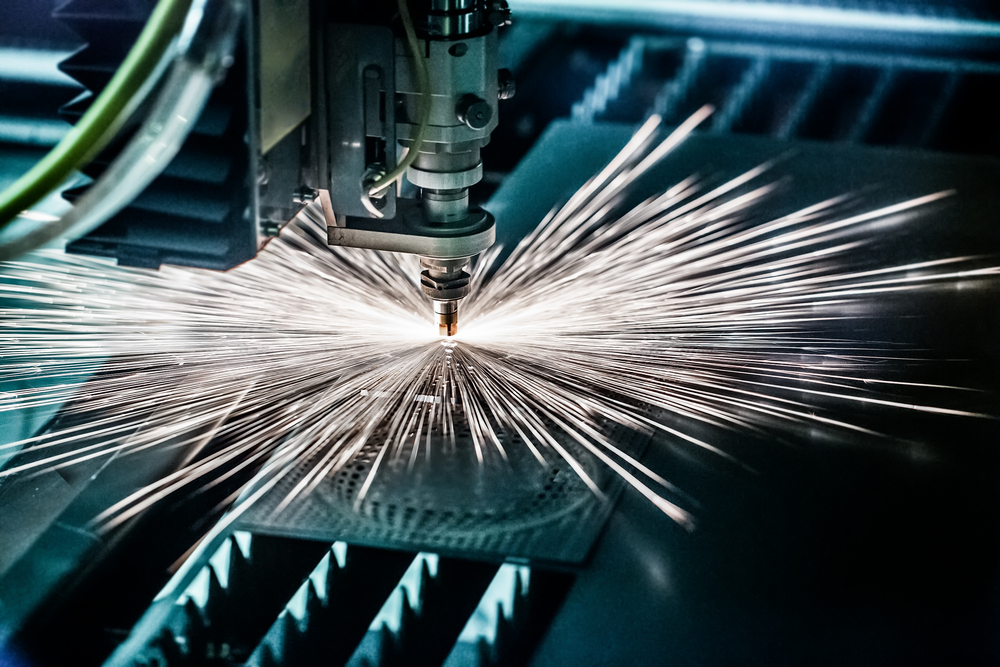
CNC technology for flat sheet metal
At present, CNC technologies (Computerized Numerical Control) are one of the most precise machining methods, and they owe their accuracy to computer control. CNC means therefore computer control of numerical devices.
Before the development of CNC machines in the 1980s, the tasks of equipment were performed by people. As you can easily guess, human work can be inaccurate and requires several inspections, but when it comes to material processing, precision and high quality are what counts, which is why CNC technology is so popular today. Customers need increasingly more complex and quality products that are best generated with minimal time and effort. Reality makes us create better and better machining tools, manufacturing methods and we optimize cutting parameters.
There are several methods of cutting out materials that we categorize as CNC techniques. The pros and cons of such methods as punching, laser cutting and water cutting are presented below.
The first stage of the product manufacturing process is the proper preparation of the material, i.e. cutting sheet metal. In the industrial sector, quality and precision are extremely important, so specialist technologies must be used.
Punching
The sheet metal punching technique is a certain technological process, thanks to which we achieve a specific shape of the sheet metal. It is usually made by means of a machine which is equipped with a die and punch (the so-called stamp). A material is placed between them and a pre-programmed device cuts the sheet in a specific way.
No additional tools such as hand scissors are needed for this process, as it is almost completely automated. Specialist presses are equipped with blanking dies, which punch a piece of sheet metal with high pressure.
Currently, this technology is very popular because of its efficiency.
Laser cutting
Laser cutting is also one of the modern methods of sheet metal processing. Interestingly, its dimensional parameters do not differ much from those of standard machining.
There is, however, a certain difference between these techniques, namely when laser cutting, we cut the material with a hot laser beam. The process also includes high-purity technical gas.
There are several methods of sheet laser cutting and their use depends on the type of cutting machine, because the material can be melted, burned or subjected to sublimation, i.e. it can go directly from solid to gaseous state.
Waterjet cutting
This CNC sheet metal cutting technology, in a nutshell, consists in cutting the material using a water jet under very high pressure. This method can replace laser or plasma, while providing the highest degree of precision. This cutting technology allows to process much thicker materials than other methods.
Waterjet cutting is relatively new, but the right machines have been instantly prepared for operation, making this technique very popular and many business owners can no longer imagine cutting without it.
Cutting out with water is possible thanks to the high pressure of the water jet, which leads to the vibration of abrasive particles which are then sucked into a mixing chamber. The water then gets into the water jet, so that the machine can cut even the hardest materials.
The water used in the process cools the material during the cutting process, which has a positive effect on its safety as it will not deform or reach a too high temperature.
Water cutting can be used when processing stainless steel and aluminium sheets.
So in conclusion, all CNC technologies are able to provide us with high quality and precision in sheet metal cutting. The choice of the appropriate technology should depend on what equipment and machines the company has at its disposal and what material is to be cut. It is also important that the employee who will have to program the machine is properly prepared and experienced.